|
Products |
General Information |
Heat Treated Glass is produced by heating the glass to a plastic state at around 650ºC, and then by computer control, the glass is moved into the quench area where it is rapidly cooled by a series of high pressure air nozzles.
This rapid cooling or quenching induces high compression stress in the glass surface, while the centre remains in tension.
Although the physical characteristics remain unchanged, the additional stresses created within the glass increases its thermal and mechanical strength.
Heat Strengthened glass is twice as strong as the annealed glass while Tempered glass is up to five times stronger than ordinary annealed glass of the same thickness. |
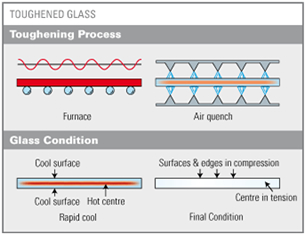 |
|
Technical Information |
Due to the internal stresses in the Tempered heat treated glass, several benefits can be achieved such as:
|
Safety
In the unlikely event of Tempered glass breaking, it fractures into small particles, significantly reducing the risk of injury.
This break-safe characteristic is an important aspect of tempered glass.
The benefits of safety glass can therefore be enjoyed, for example, along passage- ways and areas of high pedestrian traffic, in doors and adjacent panels; in shower and bath enclosures; in garden windbreaks; in balconies, balustrades and staircases. |
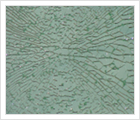 |
|
Strength |
Tempered glass has high mechanical strength and is 4 to 5 times stronger than annealed glass of the same thickness due to the stresses induced during tempering process.
It also has high thermal strength, when compared to annealed glass, can withstand a temperature differential of 250ºC, and is stable in temperatures ranging from -70ºC to 300ºC.
Tempered glass can withstand extremes of heat and cold. At 300 degrees centigrade it can be sprayed with ice-cold water and remain intact. This resistance to severe temperature differentials means that it can be used where annealed glass could be subject to breakage through thermal stress. For example, windows which for a large part of the day may be partly in shade and partly in direct sunshine.
Heat resistance combined with strength also allow its extensive use in furniture and domestic appliances.
|
Mechanical Fixing |
Tempered glass has high mechanical strength and can therefore be used with mechanical fixings, such as patch, spider, hinge (frameless), point and countersunk fixing.
|
Security |
Tempered glass is much harder to break than annealed float or laminated glass. If broken it will not provide security, however the noise due to breakage is often a deterrent.
Typical Tempered glass applications:
- Doors and Side Panels.
- Internal Partitions.
- Low Level Glazing.
- Spandrel Panels.
- Balustrades and Fences.
- Shower Doors and Screens.
- Frameless Glass Doors and Entries.
- Structural Glass Walls.
- Glass Canopies.
- Furniture.
Wherever the benefits of ordinary glass need to be combined with extra strength, safety or heat resistance, tempered glass can offer a complete and proven solution.
|
|
General Information |
Laminated glass consists of a tough plastic interlayer made of polyvinyl butyral (PVB) bonded together between two panes of glass under heat and pressure. Once sealed together, the glass "sandwich" behaves as a single unit and looks like normal glass. Annealed, heat strengthened or tempered glass can be used to produce laminated glass.
Similar to the glass in car windshields, laminated glass may crack upon impact, but the glass fragments tend to adhere to the plastic interlayer rather than falling free and potentially causing injury.
Laminated glass is the only glass to provide durability, high-performance and multi-functional benefits while at the same time preserving the aesthetic appearance of the glass. Laminated glass furnishes solutions to many architectural design problems and offers increased protection from the effects of disasters such as hurricane, earthquake and bomb blast.
|
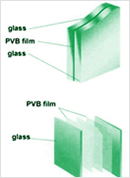 |
|
Technical Information |
Vertical Safety Glazing Applications
The Consumer Product Safety Commission (CPSC) and the architectural glazing safety sections of the major model building codes (Basic National Building Code; Standard Building Code; Uniform Building Code) all set uniform requirements for the performance of glazing materials used in applications which present a potential hazard to the public. These applications include entrance doors, storm doors, patio-type sliding doors, shower and bath enclosures, sidelights and fixed glazed panels. Performance requirements are determined by the application and the size of the glazing area. Laminated glass meets all of these established building codes.
|
Sloped and Overhead Glazing Applications |
The use of glass in sloped and overhead glazing presents a design and safety challenge. If the glass should break for any reason, the glazing system specified needs to be able to provide protection from glass fallout. With adhesion of the glass to the plastic interlayer and its ability to remain integral if broken, laminated glass has passed the requirements set of all the major model building codes in the United States and the Glazing Industry Code Committee for sloped and overhead glazing.
|
Burglaries
Burglaries are frequently directed towards targets of easy opportunity and low perceived risk by the burglar. A simple deterrent, security glazing, may be enough to send the intruder to the next easier target. Glazing materials which meet these test requirements are generally strong enough to deter a "smash and grab" burglary, and is often specified for residences, shop fronts and display cases in stores, museums and libraries. |
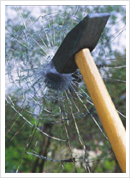 |
|
Ballistic Protection
Security glazing with laminated glass of appropriate thickness and configuration can reduce death and injury from bullets in high-risk locations, while still providing the aesthetic and visions benefits of glass.
Bullet-resistant glass is made by bonding alternate layers of glass or glass and polycarbonate to form a single, multiple-ply laminate. Laminated glass between 1" and 2" inches thick can generally resist bullets from weapons ranging from a .38 super automatic to a high power .30-06 rifle. |
 |
Bomb Blast Resistance
Unfortunately, bomb attacks and threats are on the rise all over the world. The fear generated by a bomb’s instant holocaust of property damage, injury, flame and noise can be more powerful than conventional armed attacks. Bomb blasts propagate blast energy in all directions, making buildings nearby the intended target candidates for destruction as well. Experts report that approximately 75 percent of all damage and injury from bomb blasts can be attributed to flying and falling glass following the explosion.
Laminated glass can substantially reduce injury resulting from explosions, and even reduce the cost to repair a bombed facility by reducing the extent of damage and opportunity for looting.
|
Electronic Eavesdropping
With high technology playing an increasing role in corporate and government security operations, electronic eavesdropping to obtain classified or proprietary information can result in staggering losses. Interference with computer networks from electromagnetic noise generators (such as heavy machinery operating outside the facility) can also be the source of loss.
Electronic security glazing uses PVB metalized fabric mesh and glass. When the glass is manufactured, the fabric mesh is extended an inch or more from the edge of the glass on all four sides and then connected to the metal frame. The frame members are connected to each other, and then to an effective ground. The result is a facility that is isolated from external electro-magnetic signals and occupants are capable of communicating without interception from the outside.
|
UV Protection
With time, sunlight can cause considerable damage to buildings furnishings, carpets, artwork, photographs, plants and other valuables. These items need special protection from the damaging effects of the sun’s ultraviolet (UV) rays. Laminated glass can be effective in screening out the harmful UV rays, controlling glare and decreasing solar energy transmittance.
Glazing solar control is accomplished in laminated glass by the inter-layers ability to reflect and/or absorb and re-radiate much of the solar UV radiation. Laminated glass screens out more than 99% of damaging UV light.
While protecting buildings from harmful and damaging solar UV radiation, laminated glass has no adverse affect on the health of indoor plants. In fact, laminated glass is commonly used in greenhouses and atriums to help protect flower color and reproductive development from the damaging effects of UV radiation. Photoreceptors in plants are still able to absorb sunlight which the interlayer allows to be transmitted.
|
Sound Control
Laminated glass is the sound solution to keeping unwanted noise where it belongs outside. Low-flying airplanes, highway traffic, railways, lawnmowers, or the occasional noisy neighbourhood, can make relaxing difficult. Ordinary windows are the weakest link for allowing unwanted sound to invade the home. Laminated glass offers exceptional sound control because of the sound-dampening characteristics of the plastic interlayer, regardless of the source of the sound.
|
Hurricane protection
Hurricanes are unpredictable forces within Mother Nature's arsenal of destruction. A hurricane's turbulent winds and strong gusts of air often carry wind-borne debris which can slam into glass windows and doors. Once the window panes are broken, the protective exterior "envelope" of a building is compromised, allowing strong winds to rush into a building creating internal pressurization within the structure. The trapped wind forces then push upward on the roof, outward on the exterior walls and can eventually cause complete destruction of the building.
|
Earthquake protection
Breaking and falling glass represents a major hazard in a seismic event. In moderate earthquakes, broken glass may exit the window opening, causing damage to the contents of a building. In severe quakes, falling glass can cause serious injury or death to people below the windows at street level.
While the inherent tendency of laminated glass to stay in the opening when broken is well-established, architects and engineers have only recently begun to research the performance of architectural glazing systems during an earthquake. Currently, the U.S. National Science Foundation has funded a multi-year research project at the University of Missouri-Rolla to further investigate glass performance during earthquakes. Early results indicate that annealed or heat-strengthened laminated glass has shown expected superior performance over ordinary glass in its ability to resist fallout, thus reducing the hazard to a building’s occupants and pedestrians and property below.
Test results also found laminated glass is highly resistant to the dynamic racking motions of a quake, once again helping to maintain the integrity of the buildings envelope and prevent injury and damage from glass fallout. Laminated glass also provides protection after an earthquake, as it helps to keep the building secure and weather-tight until repairs can be made. |
|
General Information |
GSI offers insulating glass, using Solar reflective glass, tinted glass, coloured films, ceramic frit patterns and Low-E coatings, filled with either dehydrated air of special gases to help designers achieve specific designs, transmission levels and solar control options. |
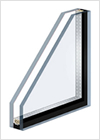 |
|
Technical Information
|
Insulating Glass Unit Construction
Insulating glass increases a window’s thermal performance. It is constructed with two or more glass panes, separated by a desiccant-filled spacer and sealed with a silicone or polysulphide sealant. The desiccant absorbs any moisture in the insulating glass unit.
The spacers have continuous corners with a single joint which gives additional protection against moisture infiltration.
|
Insulating Glass Benefits |
- Controls HVAC costs – Insulating the inner pane from extreme temperatures outside reduces air-to-air heat transfer and room-side heat gain and loss.
- Increases occupant comfort – Keeping the inner glass pane insulated from the external environment keeps the inner pane at an even temperature thus reducing the uncomfortable zone near windows.
- Lowers direct solar heat gain – Using tinted glass to control solar energy transmittance provides a lower shading coefficient and reduced glare from bright sunlight.
- Increases the Sound insulation.
|
Insulating Glass
GSI offers a big range of Insulated glass solutions using different products, providing the customers with a solution that meets the visual, thermal, and optical properties required.
GSI Technical Department offers consultants, clients and owners a free service to help engineer and provide a solution for the glass needed.
|
Installation Guidelines |
GSI recommends that all glass products provided must be installed according to the guidelines and procedures as set out in the Glass and Glazing Federation Glazing Manual and British Standard BS 6262.
Copies can be made available on request.
Warranty conditions may be adversely affected if glass products are not installed according to those codes of practice. |
|
General Information |
Since its introduction in the early 1970's, structural sealant glazing has become an increasingly popular design choice among architects.
Structural Glazing is used in the following systems:
- The “Panel system” : A conventional framing system with structurally bonded panels inserted into the grid. In this case the primary weather seal is usually silicone or EPDM gaskets.
- The “Strip-window” system : Horizontal or vertical bands with two sides of the glass bonded to a supporting structure.
The other two sides are fixed by mechanical means.
- The “Total-wall” system : Complete smooth glass wall in which the four sides are bonded to the metal supporting structure with a continuous silicone weather seal
This last system in particular has found increasing aesthetic appeal in recent years and is now frequently employed. The application of insulating glazing in a total wall system is the natural progression to this technique to ensure maximum thermal insulation to the building.
|
Technical Information |
"Structural glazing" is a system of bonding glass to the building frame with adhesive sealant in order to transfer negative and positive wind-loads to structural framing members utilising recommended silicone sealant instead of the glass being captured by conventional glazing beads. This facade design concept, results in an all-glass facade allowing a completely flush appearance to the exterior of the building, with the glass supported off the internal aluminium framing structure by the silicone sealant.
The system utilises the unique properties of silicone sealant not only for sealing the building from the elements but also for transferring structural loads from the glass to the perimeter structural support. Structural glazing techniques also allow a completely flush appearance on the exterior of the building, with the glass supported from the interior of the structure by the silicone sealant.
The strength of the bond, adhesion to both glass and metal, weather resistance and ease of application are the advantages of silicone high modulus sealant.
The basic components of a structural glazing system are:
- The structural aluminium or steel framing
- The glass
- The high modulus silicone sealant, spacers, setting blocks and gaskets
Each of these components must work in concert with the other whilst performing its primary function.
The structural framing members designed to strength requirements, similar to those found in curtain walls where deflection is a limiting factor, will normally be of extruded aluminium finished with an approved coating, applied under controlled factory conditions. This coating is a material that is compatible with silicone sealant and no other material should be used. The glass panels are designed to cope with all stress loading such as wind-loads, expansion and contraction and secured to the aluminium framing by means of the high modulus silicone sealant.
Properties
Several aluminium system providers have developed the structural glazing technique using the structural sealant to hold the glass in place, thereby completely eliminating the need for metal fasteners. As a result, the skin of the building is totally flush and presents a smooth exterior glass surface without visual interruption of conventional mullions and transoms.
The most obvious aesthetic advantage of mullion free facades can be further enhanced by the use of reflective solar control glasses on the second surface of the insulating units.
A further advantage of structural glazing units is that there will be less risk of thermal failure of the glass since the total surface is exposed and will heat up evenly. The system has advantages with regard to differential expansion of the various materials making up the building structure due to the flexibility of the silicone sealant,
The use of silicone sealant in lieu of conventional metal mullions helps eliminate problems that arise in conditions of heavy rain. A standard glazing system is susceptible to water cascading down and finding its way into metal pockets and eventually penetrating the metal grid system. By using the completely flush silicone sealant system, the water problem is minimised. In addition, the structure is rendered water and air-tight under conditions of positive and negative wind loads.
High wind and rain usually accompany low barometric pressures that increase the pressure differential on the side of the building being buffeted by heavy wind and rain - a condition that is sure to find the smallest leak point. The opposite side of the building and the sides across which the wind is blowing may have lower pressures than the interior of the building, this will exert outward pressure (suction) on windows and panels, thus a more likely ingress of water.
|
Installation Guidance |
The following parties should collaborate from the outset in the development of a project in order to achieve a successful structural glazing installation.
- Fabricator of the metal supporting structure
- Insulating glass manufacturer
- Silicone manufacturer
- Installation Contractor.
To ensure a successful installation (assuming that the framing system meets the structural qualifications specified) the drawings and loading requirements should be submitted to the glass supplier and the sealant/adhesive manufacturer for approval in writing. Upon receipt of these approvals, samples of the actual metals to which the sealant/adhesive is going to be applied, samples of the glass, samples of the spacers, and samples of the setting blocks, should be sent to the sealant/adhesive manufacturer for testing and approval.
The sealant must adhere to the metal or painted surface. The sealant manufacturer will specify what type of treatment and/or primer is required to attain the satisfactory results. It is also recommended that samples of the materials that are shipped or are on the job site be submitted for test. Often the surface of the job site material is different from the samples previously submitted for test. For example, a small change in the aluminium anodising process will change the surface adhesion characteristics. |
|
|
|
|
|
 |
|
|